Exclusive Pillow Plate Technology
Powered by New Zealand’s only flatbed laser welder.
At DTS, we’re proud to be New Zealand’s only tank manufacturer operating a flat‑bed laser welder—giving us the exclusive ability to design and produce fully bespoke laser‑welded stainless‑steel pillow plates. This advanced capability delivers outstanding thermal performance, precision engineering, and energy efficiency to clients across the food, beverage, dairy, and agri‑business sectors.
Precision Laser Technology
Laser‑welded pillow plates are created by fusing two stainless steel sheets into a sealed structure using laser welding. After welding, the cavity is hydraulically inflated, forming a patterned network of engineered bumps or corrugations that optimise heat transfer across the tank or vessel surface.
This distinctive pillow shape dramatically increases contact area and promotes turbulent flow, enhancing thermal exchange efficiency while keeping pressure loss minimal.
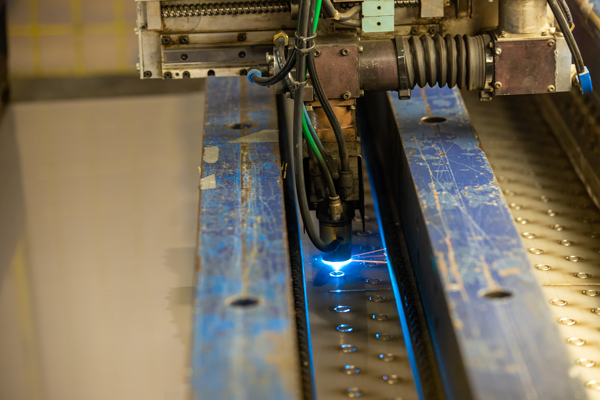
Why Pillow Plates are So Effective:
Superior Pressure Handling
Laser-welded pillow plates offer significantly higher pressure ratings, empowering engineers to tailor the pressure drop in the cooling system for maximum energy savings.
Maximum Thermal Efficiency
Internal volume is significantly reduced which leads to increased thermal efficiency and an impressive cost reduction of cooling fluid required over traditional designs.
Engineered for Turbulent Flow
The geometric embossing promotes turbulent fluid flow even at moderate velocities. This design ensures an even distribution of fluid through the entire surface, maximising heat transfer and supporting slimline tank designs that still accommodate full insulation thickness. The strategic patterning ensures fluid mixing is maintained throughout the channel.
Improved Thermal Control
With heating and cooling capabilities of up to (or exceeding) 5kW/m², our dimple pads provide precise temperature control—ideal for applications where consistency and reliability are critical.
Cost Savings
Our fully automated flatbed laser welder delivers faster lead times, reduced labour costs, and consistently high weld quality—giving you a competitive edge in both performance and price.
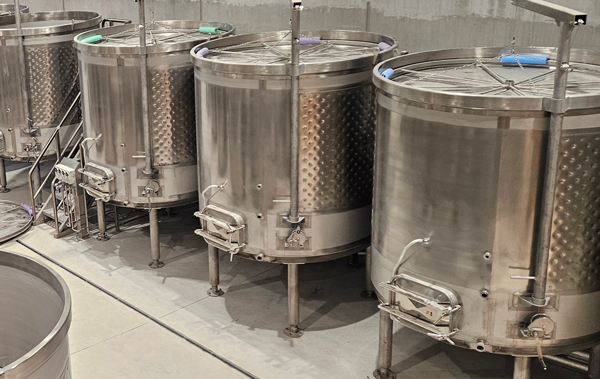